Industrial IoT System Integrators
IIoT Integration
IIoT Integration is All About The Data
IIoT integration connects thousands of smart sensors and actuators distributed throughout manufacturing plants with sophisticated software and hardware, which turns self-standing “dumb” plants into modern, smart factories.
IIoT Integration is like systems integration that were typical in the past, but with a new wrinkle. Before introducing IoT practices to the industrial environment, systems integrators would identify signals in the field and wire them back to the PLC or DCS for monitoring or control. These signals would terminate at a central location where a central processor would utilize them to make logical decisions based on how it was programmed.
Today, industrial IoT system integrators identify feedback signals in the field and wire them to smart devices. Intelligent devices have built-in computing and networking capabilities that’ll allow them to send captured signals back to a central location without additional signal wires. Further, they could be connected using a WiFi signal, Bluetooth or 5G cellular.
Are you IIoT ready? Take our free, online IIoT Plant Assessment >

Making a more decentralized and robust system
But instead of a central processor making logical decisions based on specific programming, the new IIoT integrated device uses real-time signal data and historical data to make an informed analytical decision for the manufacturing process. This data might be stored in an on-premises database, the cloud, or a combination of both.
“Manufacturing Industry in the top benefactor of IIoT at $189 billion.”
This approach may appear to be typical system integration with fewer wires; however, what makes IIoT Integration so valuable is using historical data to make real-time, analytically-driven decisions without adding extra wires and physical control hardware to an industrial environment.
What’s more, adding more wires and more physical control hardware can be very expensive since each signal has an imposed cost. IIoT tools, networking equipment, and smart sensors are the only required new components, which introduce powerful decision-making capabilities.
Leveraging Analytical Insights Using Big Data
Before smart factory and the Industrial Internet of Things, the only concern was ensuring the wiring was correctly done so scaling could be achieved. Now, smart hardware must be configured individually and then communicate back to a central brain through the network. This central brain will be programmed to handle controls but also leverage AI and Big Data analytics to make real-time decisions, which creates more digital complexity. Therefore, the digital infrastructure must be configured to handle the increased traffic.
If the new IIoT system isn’t properly integrated, owners and managers are left with individual skids and components that can’t communicate. Islands of components are of no benefit to the companies since they aren’t gathering the data and making meaningful decisions. Proper IIoT Integration is all about the implementation of a logical decision-making process, and that begins with knowledgeable communication infrastructure, paths and protocols.

Manufacturers Biggest Challenges Are Reducing Labor, Power and Operating Costs; Preventing Downtime
Manufacturing leaders face a wide range of challenges that must be addressed. Most are looking for ways to reduce labor, power and operating costs. Additionally, manufacturers want to improve production throughput while reducing manufacturing downtime. A Forbes Insight survey found that nearly 50% of companies that went through an IoT business transformation, increased profits by 5–15%.

Reduce downtime
Studies reveal 82% of manufacturers have experienced at least one unplanned downtime outage in the last three years. What’s more, Aberdeen estimates the average cost of downtime is $260,000 per hour. The ability to predict machine maintenance via IIoT technology helps reduce downtime significantly.

Eliminate siloed systems and databases
Many manufacturers are saddled with hundreds of siloed systems and databases that can’t communicate with one another. IIoT integration eliminates information silos and connects all inputs to a shared cloud backbone. During the IIoT integration journey, some manufacturers have even recovered their IIoT investments in as little as 12 months.
How to Make Informed Decisions Based on Analytical Insights and Collected Data
Historically, many plant managers collected manufacturing data but failed to leverage that data. Today, however, you can instantly make informed decisions using AI and analytics driven, not only by your collected data but also the data on your system parts or components.
With new technologies and the best available digital tools, you can stop managing your factories and machines on unreliable gut instincts to keep production running. With IIoT Integration, your decisions will be backed by analytics and data.
Results Engineering Can Help You Make the Leap to Data-Informed Decisions and Higher Productivity
An integrated IIoT/Smart Factory will increase production, predict & prevent maintenance downtime, and reduce operating costs, especially labor. With integrated real-time data on connected smart sensors throughout your plant you can move from making “Gut-Feel” decisions to informed data-driven decisions. ROI is available for companies with any size plants, system-wide or a single process. In fact, it is predicted the economic impact of IIoT/Smart Factory implementations is $11 Trillion by 2025 (McKinsey & Co.)
Results Engineering has chosen 30 top questions from its main IIoT engineering audit to form a free assessment allowing you the first insights on how IIoT ready your plant is.
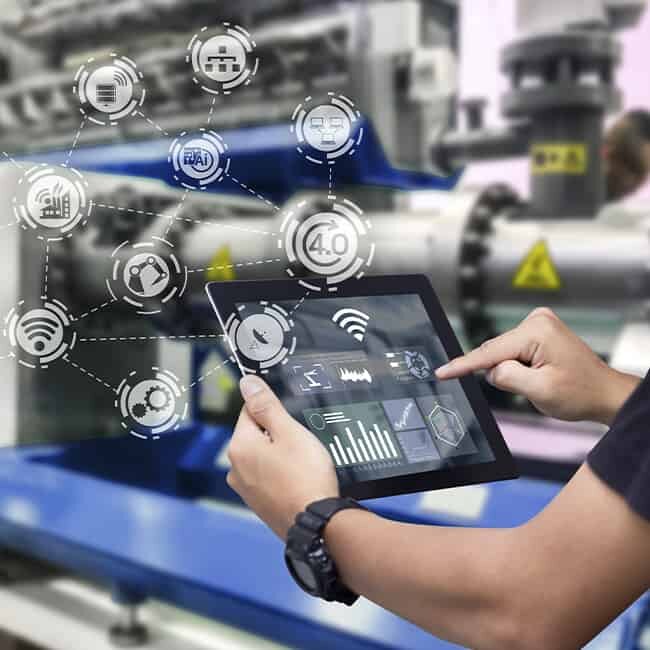
We Are Making The Unknown Known Through Advancements in Data
Results Engineering is an Edge-to-Cloud IIoT Systems Integrator that has been working in automation & controls for the last 33 years. Our role is to guide our clients on the path to smart factory implementations, achieving ultimate plant control.
Take the next step, get your IIoT Plant Assessment!
Manufacturers have no idea how impactful IIoT/Smart Factory is to their plants.
Results Engineering created a free plant assessment to solve that problem. 30 questions and 30 minutes will reveal all you need to know.

Latest Articles
What is Industry 4.0 and How is it Different from IIoT
What is Industry 4.0? This is a more complex question than a simple answer will satisfy. Industry 4.0 is the new age of manufacturing. This new age is a departure from the computer and automated systems in...
How to Improve Cybersecurity in Manufacturing
With the rapid increase in the number of connected IIoT devices within a manufacturing environment and across an enterprise, the opportunity for risks of cybersecurity in manufacturing facilities increases with each...
Greenfield VS. Brownfield Smart Factory
The strategy for deployment of a new manufacturing IIoT initiative must first include identification of a brownfield or greenfield deployment. While a greenfield strategy will take place in a new installation that can...